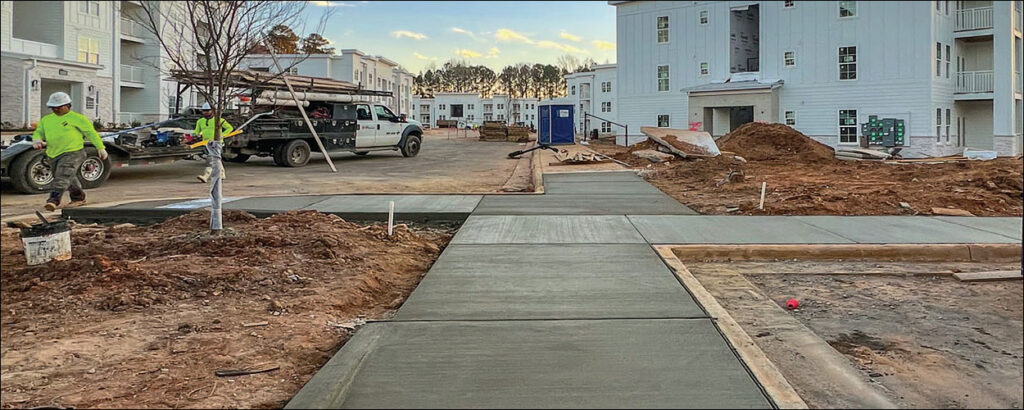
Understanding Commercial Concrete Construction
Concrete is one of the most widely used building materials in the world. Strong, durable, and versatile, it’s found in everything from sidewalks and bridges to skyscrapers and stadiums. But not all concrete work is the same. This article discusses commercial concrete contracting, the role of commercial concrete contractors, and how this essential trade supports the future of growing communities.
What is Commercial Concrete Construction — and How is it Different from Residential Concrete Construction?
Commercial concrete construction involves the planning, forming, pouring, and finishing of concrete structures designed for commercial, industrial, or municipal use.
These projects are typically larger in scale, more structurally demanding, and subject to stricter engineering standards than their residential counterparts. Commercial concrete structures must support heavy loads, endure constant use, and often meet complex regulatory requirements.
From industrial slabs to sidewalks, access ramps, and public infrastructure, commercial concrete construction requires specialized equipment, skilled crews, and precise coordination with architects, engineers, developers, and local inspectors.
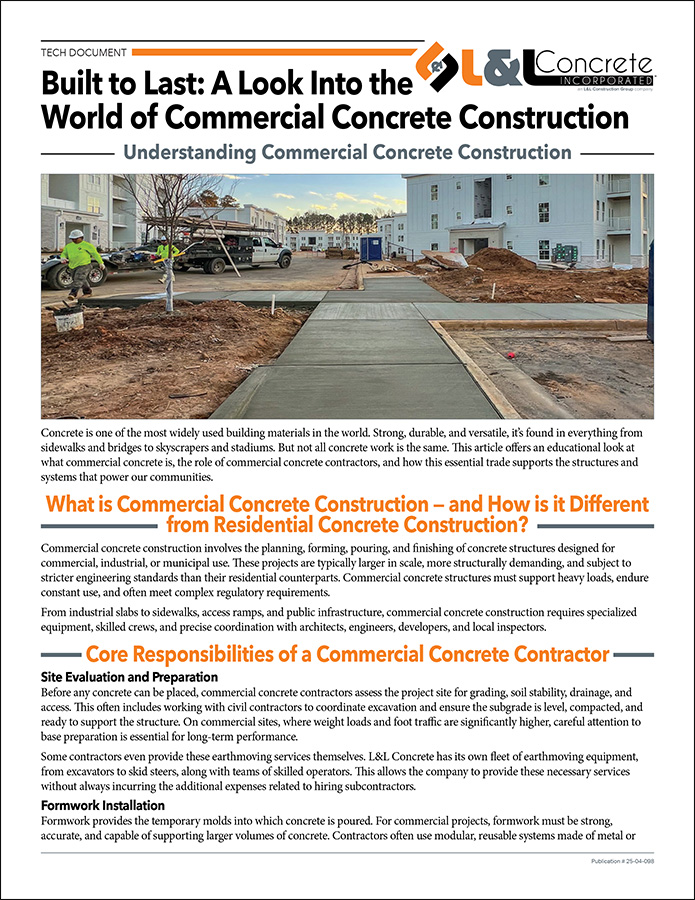
Core Responsibilities of a Commercial Concrete Contractor
Site Evaluation and Preparation
Before any concrete can be placed, commercial concrete contractors assess the project site for grading, soil stability, drainage, and access. This often includes working with civil contractors to coordinate excavation and ensure the subgrade is level, compacted, and ready to support the structure. On commercial sites, where weight loads and foot traffic are significantly higher, careful attention to base preparation is essential for long-term performance.
Some commercial concrete contractors are able to provide earthmoving services themselves. L&L Concrete has its own fleet of earthmoving equipment, from excavators to skid steers, along with teams of skilled operators. This allows the company to provide necessary excavation and grading work in-house, without always having to incur additional expenses related to hiring subcontractors.
Formwork Installation
Formwork provides the temporary molds into which concrete is poured. For commercial projects, formwork must be strong, accurate, and capable of supporting larger volumes of concrete. Proper formwork is critical to achieving the structural integrity required in commercial settings.
Reinforcement Placement
Because concrete alone is strong in compression but weak in tension, reinforcement is a key component. Commercial concrete contractors often must install steel rebar, wire mesh, and sometimes post-tensioning systems to strengthen the concrete against heavy loads and prevent cracking. Correct placement, spacing, and securing of reinforcement materials are essential for the finished structure to perform as designed.
Concrete Pouring and Finishing
Concrete is placed using a variety of methods, including pumps, chutes, and crane buckets, depending on the project size and site layout. Once poured, the surface is leveled and finished to meet specific performance and aesthetic requirements. Commercial finishes may need to be highly durable, slip-resistant, or architecturally uniform, especially for public spaces or industrial floors.
Code Compliance and Safety
Commercial concrete work must adhere to rigorous building codes and safety regulations. Contractors are responsible for ensuring that their work meets structural load requirements, fire resistance standards, and stormwater management protocols. A major focus is compliance with the Americans with Disabilities Act (ADA). ADA-compliant work includes precise slope measurements for ramps, proper curb and gutter transitions, detectable warning surfaces at pedestrian crossings, and slip-resistant finishes to ensure accessibility for everyone. Mistakes can lead to costly repairs, liability issues, and unsafe conditions, making accuracy a top priority.
Typical Types of Commercial Concrete Projects
Footings and Foundations: These are the structural base elements that support buildings, retaining walls, light poles, and other vertical loads. Commercial footings are engineered to handle higher weight and are often deeper and wider than those found in residential construction.
Parking Lots and Loading Docks: These large surface areas must be designed to support constant vehicle traffic, including heavy trucks and delivery equipment. Contractors pay special attention to drainage, surface finish, and jointing to prevent cracking and deterioration over time.
Industrial Floors: Found in warehouses, manufacturing facilities, and distribution centers, these floors must be perfectly level, extremely durable, and able to handle machinery, forklifts, and high point loads. Reinforced slab-on-grade systems are common, often with fiber additives or post-tensioned cable reinforcement for added strength.
Sidewalks, Curbs, Gutters, and Medians: These are critical components of public infrastructure and urban design. Commercial concrete contractors construct them with precision to ensure proper drainage, pedestrian safety, and visual consistency across long stretches of roadways or campus environments.
ADA-Compliant Access Ramps: Accessibility is a major consideration in commercial concrete work. Ramps must be built to exact slopes and dimensions to comply with the Americans with Disabilities Act (ADA). These include handrail-ready landings, tactile warning strips at curb ramps, and non-slip surfaces—features that not only meet legal requirements but also serve the broader public.
Collaboration with Developers
Commercial concrete contractors often work closely with real estate developers and site development contractors, particularly in the early stages of new subdivisions, mixed-use developments, and planned communities. Their role includes building the interconnected networks of sidewalks, driveways, curbs, gutters, and access ramps that form the backbone of a community’s infrastructure.
Concrete crews coordinate with grading and utility teams to install sidewalks and multi-use paths according to detailed plans, ensuring proper slope for drainage and ADA compliance. Driveways connecting individual lots to public roads are poured with attention to both durability and curb appeal. Curbs and gutters are critical for channeling stormwater runoff, protecting streets and landscaped areas from erosion and flooding. Medians and traffic islands are also constructed using commercial concrete methods, providing both functional and aesthetic benefits.
Through this collaboration, commercial concrete contractors help bring master-planned environments to life, delivering the durable infrastructure that supports neighborhoods, businesses, and public spaces for generations to come.